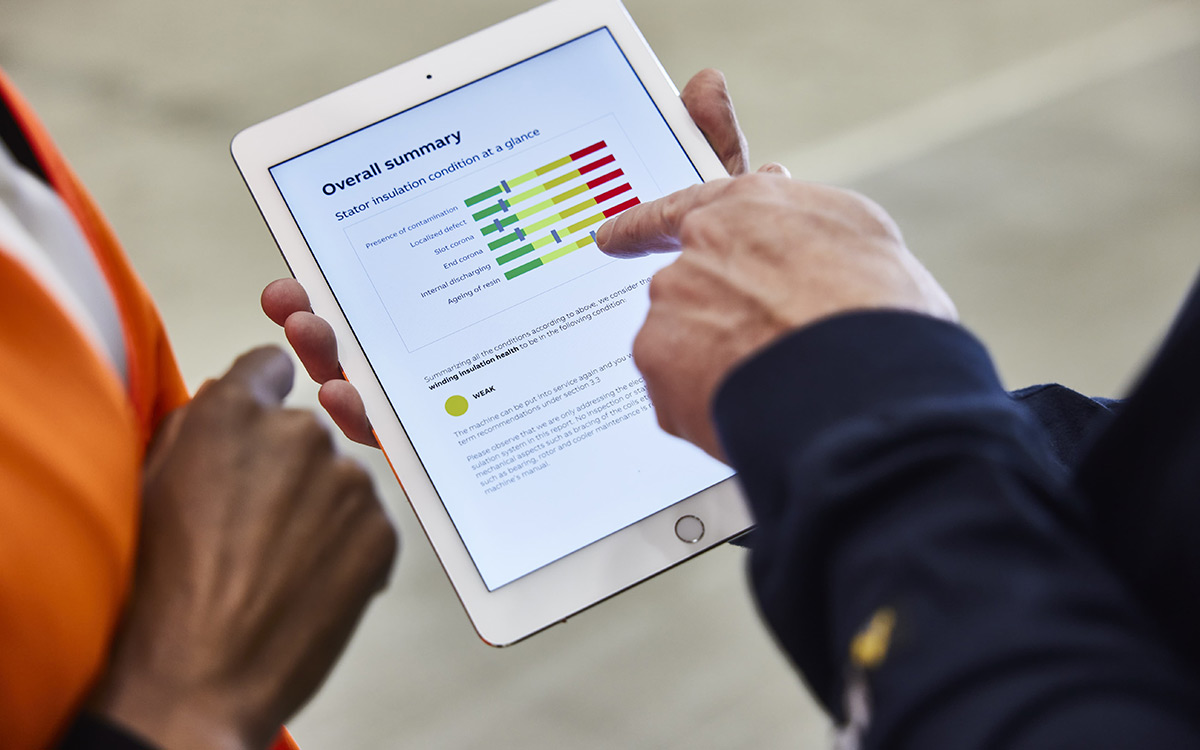
El gran error de la industria peruana: esperar a que los motores fallen4 min lectura
Escrito por Ing. Diego Arias, especialista en servicios del negocio Motion de ABB en Perú
Cada hora de inactividad no planificada es tiempo y dinero perdido. Mientras el mundo avanza hacia la digitalización del mantenimiento, en Perú las industrias siguen apostando por estrategias reactivas que disparan los costos y reducen la eficiencia de equipos que son el corazón de sus procesos: los motores y generadores de alta tensión.
En la industria, el peor enemigo no siempre es el que se ve venir. En Perú, cada año, paradas imprevistas en motores de alta potencia generan pérdidas millonarias que, en promedio podrían oscilar los US$ 125 mil cada hora, afectando la competitividad de sectores clave como la minería, manufactura y energía.
Sin embargo, mientras en otros países la digitalización del mantenimiento de motores y generadores de alta tensión es una práctica que se está consolidando. En Perú, su implementación aún es limitada ¿Por qué seguimos reaccionando ante las fallas en lugar de anticiparnos a ellas?
Un problema invisible
El 60% de las averías en motores de alta tensión ocurre en el bobinado del estator, una pieza fundamental para su funcionamiento. Estas fallas no se detectan a simple vista y, cuando se manifiestan, ya han generado un daño significativo. La contaminación, la temperatura, los esfuerzos eléctricos y mecánicos además del envejecimiento natural aceleran su deterioro, y muchas veces los diagnósticos llegan tarde.
Frente a este panorama, existe un servicio digital en Perú: el “Programa de Análisis de Expectativa de Vida” (LEAP, por sus siglas en inglés), que permite evaluar la condición actual del aislamiento del bobinado y expectativa de vida útil con hasta un 90% de confiabilidad. A través de pruebas especializadas, que toman entre 4 a 6 horas, además de las pruebas eléctricas realizadas, se recopilan datos clave como la temperatura de operación, número de arranques y paradas del motor o generador. Luego, expertos del Centro de Excelencia de ABB analizan esta información y generan un informe con recomendaciones concretas a corto y largo plazo de operación y mantenimiento, como la reparación de descargas parciales, limpieza localizada o el rebobinado del estator. Recomendaciones que tienen la finalidad de extender la vida útil de estos equipos.
Los motores grandes de alta potencia son el corazón de muchas operaciones industriales. A diferencia de los motores de bajo voltaje, que pueden ser reemplazados con relativa facilidad, los motores y generadores de alta potencia son costosos, hechos a medida y requieren largos tiempos fabricación, instalación y puesta en marcha. Esto significa que cualquier falla inesperada puede representar pérdidas millonarias y afectar la productividad de toda una planta. Por ello, maximizar su vida útil mediante un mantenimiento basado en la condición no es solo una recomendación, sino una necesidad estratégica.
El costo de no actuar
Los beneficios de LEAP están comprobados. Basado en más de 10 mil mediciones a motores y generadores de alta tensión de ABB y otras marcas en alrededor de 40 países, se ha revelado que con LEAP, las paradas no planificadas pueden reducirse hasta en un 35% y, si se gestiona correctamente algunas condiciones operativas como la temperatura del bobinado, su vida útil se extiende en un 28%. Esto no solo optimiza el retorno de inversión, sino que también mejora la disponibilidad operativa de las industrias.
A pesar de esto, en Perú el monitoreo basado en condición aún no se aplica masivamente. Mientras que el 99% de las empresas globales reconoce el valor de la digitalización en el mantenimiento de motores y generadores de alta potencia, muchas compañías locales siguen apostando por estrategias reactivas que elevan los costos de operación y afectan la continuidad del negocio.
¿El futuro del mantenimiento?
El mantenimiento basado en condición no es una promesa futurista, sino una necesidad urgente para la industria en Perú. LEAP ha demostrado su eficacia en la reducción de tiempos de inactividad y la optimización del rendimiento de motores y generadores de alta tensión. La resistencia al cambio, el desconocimiento y la falta de inversión en digitalización están costando millones a las industrias, afectando su competitividad en un mercado global cada vez más exigente.
La transformación ya está en marcha en otros países, y las empresas peruanas no pueden quedarse atrás. Apostar por servicios digitales, como LEAP, no solo protege la inversión en equipos industriales, sino que también garantiza la continuidad operativa y la eficiencia energética. La pregunta no es si se debe hacer el cambio, sino cuánto más se está dispuesto a perder antes de tomar acción.